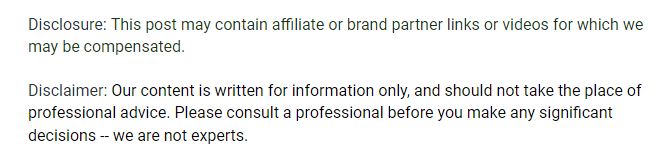

With the rise of industrial CT scanning has come a much easier way of testing and developing products in the field before they get to the market. This can save companies time and money, not to mention make the buying and searching experience much better and more streamlined for the customers. Wall thickness analysis, among many other types of assembly analysis, is one of those things that has come out of industrial CT scanning services.
A wall thickness analysis is specifically designed to help identify any variations in wall thickness, which ends up costs the manufacturer a lot of money, especially if they are producing large amounts of a product with that particular defect.
Most products simply must have a certain thickness in order to be structurally sound, and withstand pressure, as many of them need to be. Wall thickness analysis allows you to have your product scanned, and places where the wall thickness is varied can be noted and changed in later prototypes.
Indeed, this scanning process allows manufacturers to cut down on production and inspection costs. It can also decrease failure analysis costs by between 25% and 75% compared to current technologies.
Basically, CT, or computerized tomography, scans use the data from several x-rays in order to combine them and create one 3D image. Since this method is noninvasive, there is no need to damage a sample or a prototype, and it is also possible to understand a machine or a part of the machine while it is motion. And, x-rays can be taken as fast as 30 frames per second. This process if fast and highly accurate.
Indeed, industrial CT scanning allows manufacturers with prototypes to make sure that their products are safe, cost effective, and correct. It is no mystery why many big manufacturers now make it a necessity to get their products industrially scanned, with assembly analysis or wall thickness analysis.