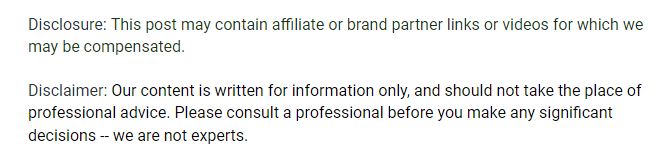
In the pharmaceutical industry, a lot of work gets done on a daily basis that can have massive importance when you consider the health and wellbeing of millions of people around the world. Saving lives is something that needs to be done right and this is why these companies put in a lot of effort in ensuring that the conditions that can make the inherent processes safer and more likely to succeed are all in place. With GMP standards and GMP quality control properly enforced, a lot can be achieved in making facilities engaged in drug development or manufacture safer and more secure.
If you run or manage a business that operates in this industry, it is likely that you already understand and appreciate the importance of maintaining exacting standards in your facilities for drug development and manufacture. Apart from making sure that your product quality can remain excellent and you can keep everything safe and healthy, there can also be a number of compliance issues that you would need to sort out to operate in these industries. Achieving proper compliance would mean a thorough knowledge of GMP storage conditions and clean room standards and making sure that those standards are always met in your facilities.
When it comes to drug development and manufacturing facilities, it can become very important to be able to precisely control all the parameters that create the interior conditions of such facilities. Apart from granular control over temperature and humidity levels, you would also want to control the quality of air inside these facilities in order to avoid contamination of any kind. Contamination can result in major losses by skewing up your results and can also render the working environment unsafe for the development and manufacture of drugs. This is why GMP storage conditions and clean room standards can become very important.
With the issue of air quality, there can be a number of things that you would need to know. For example, outdoor air can contain an average of 35 million particles the size of half a micrometer and above per cubic meter. In a clean room, you would need to ensure that there are no particles that size in the air. Further, you would have to limit the number of particles of the size 0.3 micrometers and smaller to fewer than twelve. Similarly, the tolerances can be extremely low when it comes to dealing with humidity levels with margins often hovering close to 1% either way.
Fortunately, there can be a number of tools and techniques you can employ to ensure that modern clean room standards are adhered to in your facilities. A range of sensor equipment can be used to keep a handle on temperature and humidity levels that can allow you granular control and provide you with alerts when something gets out of range. Similarly, the air quality inside the clean rooms can be kept within the specified parameters through the use of advanced filtration equipment, fume hoods, and air quality sensors. These systems need to work in tandem to ensure the perfect environment at all times.
Once you have deployed the right tools and measures that can help you enforce and maintain clean room standards, you would also need to make sure that the equipment is properly maintained and regularly inspected so that you can enjoy reliable performance over the long term. For example, fume hoods that you install in your clean rooms need to be assessed at least once a year through the help of an independent certifier in order to ensure that it has the right amount of air moving capability in order to serve its purpose. Similarly, other important components in your clean rooms need to be regularly assessed as a single malfunction can prove to be costly.
Keeping these important points in mind, it can be a good idea to understand what is at stake and make every effort to ensure good clean room standards are met and the best practices adopted to keep things that way. This can be a great thing overall for your drug company.